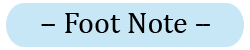
The simplest classification of lubricants classifies them as
being Internal and External, based on their relative
compatibility with PVC primary particles. Many lubricant
molecules have a polar head and a non-polar tail, with very
different attractions for each end, as in the case of
surfactants. Polar headed waxes such as fatty alcohols,
fatty acids (Stearic Acids) fatty esters and fatty amides
have moderate compatibility in PVC and are characterised as
internal lubricants. Non-polar waxes like paraffin and
polyethylene are incompatible with PVC and are called
external lubricants.
Internal lubricants reduce the frictional forces occurring between the PVC molecule chains, thus reducing melt viscosity. They are polar and thus are highly compatible with PVC. They help achieve excellent transparency even at high dosages and do not tend to exudate, which helps optimizing welding, gluing, and printing properties of the final product.
External lubricants reduce the adhesion between PVC and metal surfaces. They are mostly non-polar such as paraffin and polyethylene waxes. The external lubrication effect is largely determined by the length of the hydrocarbon chain, its branching and its functional group. At high dosages they can lead to cloudiness and exudation
Non-polar, Polar and film forming are the three main
classifications of lubricants for PVC based on their modes
of operations.
PVC lubricants can also be categorised according to their
origins, principally four – petroleum, synthetic
hydrocarbon, mineral and some natural vegetable based
triglycerides.
Petroleum waxes consist of two types. First, Paraffin waxes
(which are macro crystalline, containing primarily linear
alkanes in the C20 to C40 range and are hard and brittle
with melting range of 45 – 70 deg C. Second types are
Microcrystalline waxes which contain significant quantities
of cyclic and branched chain alkanes in the C30 to C80
range, and are soft, tough and have high affinity for oil.
They melt in the range of 45 to 70 deg C. Petroleum waxes
for PVC also include waxy petroleum oils that work as
excellent external lubricants.
Synthetic Hydrocarbon waxes used in PVC are basically of
three fundamental types. They include Polyethylene wax,
Oxidised Polyethylene wax and synthetic Paraffin wax also
known as Fischer-Tropsch wax. The most popular and effective
Polyethylene waxes have a melting range of 98 – 115 deg C.
Their oxidation results in chain scission at their branch
points resulting in the formation of a wide array of
oxygenated products including acids, alcohols, esters,
aldehydes, ketones and hydroperixides. The resulting
Oxidised PE waxes are much more polar, more compatible with
PVC and act as film formers in PVC melts. Fischer-Tropsch
waxes are microcrystalline, water white, oil free, hard and
with high melting points. They are often blended with
natural paraffins to raise their melting points. Due the
better dielectric constant, electrical resistance and
electrical breakdown strength of FT waxes compared to other
petroleum waxes, they are preferred for production of cables
and wires.
Mineral waxes are principally derived from Montan Wax which
is a fossilised vegetable wax. Over past several years, Montanic acid and its esters and soaps have found wide use
in PVC for high tech plastic lubricant applications. Their
combination of high molecular weight, film forming
properties and plate out resistance is unequalled by
alternate lubricants. Ethylene glycol montanate and
partially saponified 1,3 butanediol montanate are excellent
examples.
PVC lubricants produced from naturally occurring
triglycerides can be considered to be derivatives of
1-Octadecanoic acid, commonly called Stearic Acid, a linear
saturated carboxylic acid having 18 carbon atoms. Stearic
Acid can be converted into a wide variety of lubricants. In
many instances, there are more variety of complex ester
lubricants on the market than there are discernable
advantages.
Polar lubricants are hydrocarbon compounds containing polar
functional groups such as alcohols, esters and amides. They
orient in PVC melts with polar head attracted to PVC.
Examples are Stearyl Alcohol, Glycerol Monostearate, Stearyl
Stearate, Montan ester, etc. When interchanging polar-headed
lubricants, considerations should be based upon functional
groups, molecular weights, melt viscosities, volatility and
melting points.
For flexible PVC compounds, one type of lubricant, a film
former, is generally sufficient for most lubricant
applications, because the presence of ester based
plasticizer acts as a polar headed lubricant. Occasionally,
however, a speciality purpose polar-headed lubricant, such
as GMS, is beneficial for imparting a special ancilliary
property such as fog resistance to a flexible vinyl film.
For rigid PVC applications, as a general principal, PVC
lubricant systems of a single class are not as effective.
Often, all three classes, namely polar, non-polar and film
formers are required to achieve optimal results. Balub class
of lubricants work on this principal to give the best
results.
|